OSHA’s Top 10 Most Cited Health and Safety Violations of 2024 a Deeper Look!
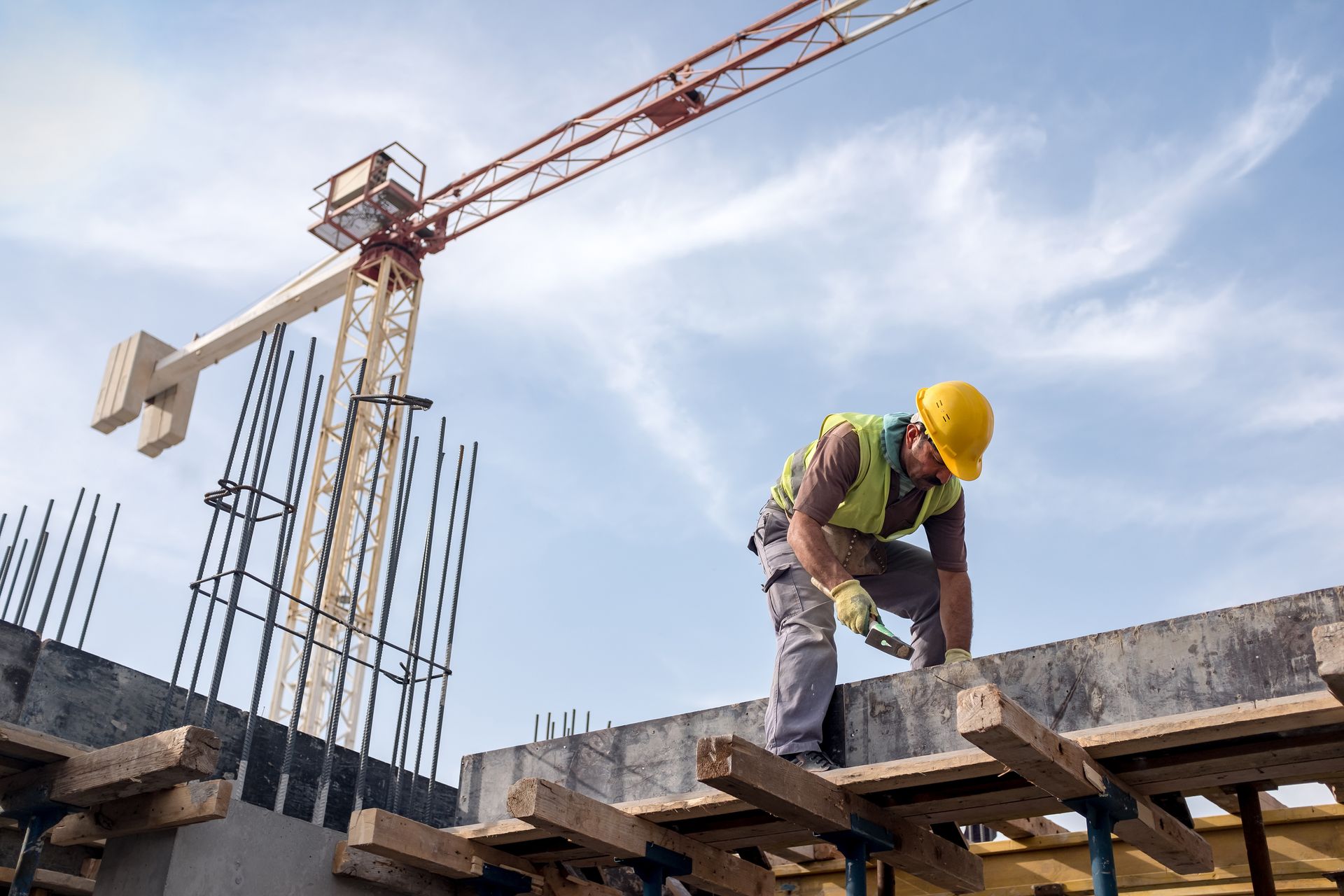
Each year, as the Occupational Safety and Health Administration (OSHA) releases its list of the top 10 workplace safety violations, a pattern emerges that begs a question: Are these frequent violations a sign that employers continue to struggle with the same safety issues, or does it reflect a disposition among OSHA inspectors to focus on areas where they are trained to focus?
The Persistent Issue of Repeated Findings
The repetition of certain violations year after year might seem surprising, but it underscores a significant challenge in workplace safety management. The top violations tend to be those that are most visible and easiest to spot during inspections, such as fall protection and hazard communication. This consistency suggests that while awareness is high, practical implementation and adherence to safety practices lag behind.
Top 10 Most Cited Health and Safety Standards of 2024
1. . Fall Protection, General Requirements: 6,307 violations
For the 14th consecutive year, fall protection tops the list of OSHA's enforcement priorities. This emphasis is not arbitrary; OSHA has designated fall protection as a national emphasis area, making it a primary focus during inspections. It's often one of the easiest violations to spot without extensive investigation skills. The OSHA standard 1926.501 mandates that employers must provide fall protection systems like guardrails, safety nets, or personal fall arrest systems for workers at risk of falls of six feet or more in construction and four feet in general industry.
Often, the major factor in these violations is human behavior. Many offenders might think, "No one is watching, and this will only take a moment, so it's no big deal." However, this mindset can lead to non-compliance with critical safety measures, putting worker safety at significant risk.
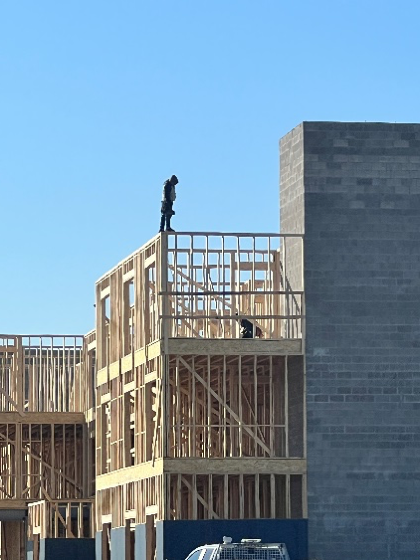
Figure 1 I saw this last week while exiting a fast food establishment.
2. Hazard Communication: 2,888 violations
This has been on the top 10 list I believe since its conception. Why? Once again it is so easy to find these violations and even a rookie inspector can win big with these finds. At the heart of Hazard Communication is OSHA standard 1910.1200. This important regulation ensures that employees are fully informed about the hazards associated with the chemicals they work with. Common slip-ups in this area include not having a comprehensive written hazard communication program, insufficient training on hazardous chemicals, and missing or outdated Safety Data Sheets (SDSs). Each of these components is crucial for maintaining a safe working environment, and their importance cannot be overstated. Let's dive deeper into why staying vigilant about Hazard Communication is key to a safer workplace!
3. Ladders: 2,573 violations
Ladders accounted for 2,573 safety violations last year. While I've encountered some exceptional ladder safety programs—where each ladder is numbered, inspected, tagged, and stored securely in a designated area—unfortunately, these are the exception rather than the rule. More often, I see neglected safety programs where ladders go uninspected and continue to be used well past their safe operational life. According to OSHA regulation 1926.1053, it's crucial for employers to ensure that ladders are not only used properly but are also securely fastened and maintained regularly. A common issue found in violations of this standard, specifically 1926.1053(b)(1), is failing to extend portable ladders at least 3 feet above the landing surface. When extending the ladder isn't feasible, securing it with a grasping device is a must to ensure safety.
4. Respiratory Protection: 2,470 violations
OSHA's standard 1910.134 mandates that employers provide respirators to employees when needed to protect them from harmful airborne contaminants. Common violations of this standard include failing to offer necessary medical evaluations, not implementing a comprehensive respiratory protection program, and neglecting to ensure the use of properly fitting facepieces.
Pro Tip: Always take a moment to read the safety pamphlet insert that comes with your respirator. Most of the safety pamphlets start by reminding you that, before using a respirator in a contaminated area, you must perform either a qualitative or quantitative fit test as specified by OSHA 29 CFR 1910.134 or CSA Standard Z94.4—essential safety information indeed! Digging deeper into the pamphlet, you’ll find that the manufacturer sets exposure limits based on the type of fit test conducted.
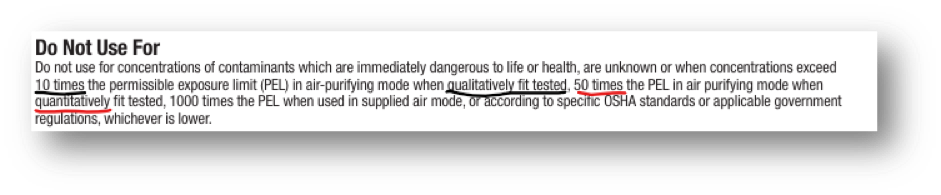
For instance, with a qualitative fit test, you're approved for exposure up to 10 times the permissible exposure limit (PEL). However, a quantitative fit test raises this approval to 50 times the PEL. This detail is a gem for inspectors and highlights a critical point from Safety Psychology: very few people take the time to read this pamphlet, potentially missing out on crucial safety guidelines. OSHA will check this every time.
5. Lockout/Tagout: 2,443 violations
OSHA standard 1910.147 mandates that employers establish procedures to safeguard workers from accidental machine start-ups or energy releases during maintenance. Violations frequently cited include shortcomings in energy control procedures, inadequate training and communication, and insufficient periodic inspections.
While compliance challenges persist, it’s encouraging to see a significant uptick in safety practices, particularly in the area of lockout/tagout processes. Many companies are now prioritizing the refinement of their safety protocols, enhancing training programs to ensure that all employees understand how to effectively control hazardous energy, and committing to regular audits of their procedures. This proactive approach not only helps in meeting OSHA requirements but also significantly boosts overall workplace safety, demonstrating a growing industry commitment to protecting workers from potential injuries or worse. Let’s keep this positive momentum going and continue to seek out opportunities for improvement in our safety practices.
6. Powered Industrial Trucks: 2,248 violations
OSHA standard 1910.178 strictly mandates the safe operation of forklifts and other industrial trucks. Frequent violations of this standard include unsafe vehicle operations and the failure to provide refresher training or evaluations.
A concerning aspect often overlooked in many workplaces is the occurrence of 'near misses,' which are seldom reported. Near misses, where an incident could have resulted in an injury or property damage but narrowly avoided, are critical indicators of potential hazards. Their underreporting can mask underlying safety issues, allowing risks to go unaddressed until a serious accident occurs. This lack of reporting and attention not only increases the hazard potential but also misses vital opportunities for corrective action. By encouraging a culture that actively reports and analyzes near misses, organizations can significantly enhance their safety protocols, preemptively addressing risks and reinforcing a commitment to worker safety.
7. Fall Protection, Training Requirements: 2,050 violations
Fall Protection, under OSHA standard 1926.503, requires employers to provide training for employees exposed to fall hazards. In 2024, the most common violations were due to the failure of employers to implement a fall protection training program. It's critical to note that fall protection has been the number one issue cited by OSHA for 14 consecutive years.
With today's resources like Learning Management Systems (LMS), training matrices, and varied training platforms—ranging from traditional on-site instructor-led and online instructor-led, to self-paced online courses—there's no excuse for not having properly trained employees. Failing to provide adequate fall protection training is not just a regulatory misstep; it's a significant legal liability. Inadequate training can lead not only to hefty OSHA fines but also to severe civil penalties following an incident.
For example, in recent years, there have been numerous cases where companies faced substantial financial losses due to civil lawsuits following fall-related incidents. Companies have been penalized millions of dollars in damages for failing to ensure the safety of their employees, highlighting the crucial need for compliance and proper training to mitigate these risks effectively. These cases serve as stark reminders of the potential consequences of neglecting safety training, underscoring the importance of a proactive approach to workplace safety.
8. Scaffolding: 1,873 violations
OSHA standard 1926.451 thoroughly outlines the requirements for scaffold design, construction, and use, ensuring worker safety. Common violations include the absence of fall protection for workers on heights over 10 feet (what – Fall Protection again ☹), inadequate foundation support, incomplete planking or decking, and the lack of proper access methods.
These issues are not just critical safety hazards but also represent "low-hanging fruit" for OSHA inspectors or any safety auditors due to their high visibility on worksites. The presence of such violations can be easily spotted, making it more likely for companies to face inspections and penalties.
To enhance safety and compliance, employers need to provide strong fall protection (what another fall protection bit) to be sure scaffolds are built on solid foundations, complete all decking, and furnish proper, safe access methods such as ladders, stair towers, or ramps securely attached to the scaffolds. Addressing these visible issues not only helps in meeting OSHA's stringent requirements but also plays a crucial role in preventing serious injuries and fatalities on construction sites.
9. Personal Protective and Lifesaving Equipment – Eye and Face Protection: 1,814 violations
Under OSHA standard 1926.102, it's essential for employers to equip their workers with the right personal protective equipment (PPE) for hazards like chemical splashes or flying particles. While many employers are great at providing PPE, sometimes there's a gap in ensuring it's the best fit for the specific risks involved. This often happens when choices are based more on what's easily available or what safety supply vendors recommend rather than what's most suitable for the job.
Another common issue is how PPE is worn. It's not unusual to see safety glasses, but instead of protecting eyes, they’re resting on someone's head. This points to a need for better training and supervision. Employers should focus not just on supplying the correct PPE, but also on making sure everyone understands how and why to wear it properly. Regular training sessions can really help drive home the importance of using PPE correctly, ensuring workers are both safe and compliant with safety standards. This proactive approach is a simple yet effective way to minimize risks and keep everyone protected on the job.
10. Machine Guarding: 1,541 violations
OSHA standard 1910.212 mandates that employers must install proper machine guards to prevent worker contact with moving parts. Common violations include using inappropriate types of guards and inadequate guarding at points of operation. Interestingly, there has been an uptick in safety compliance in this area compared to previous years, which is encouraging to see. However, this improvement raises a critical question: Are there genuinely fewer violations, or is OSHA not scrutinizing as closely as before? It's essential for employers to not only comply with safety regulations but also to consistently maintain and reassess their safety measures to ensure ongoing protection for all workers.
Takeaways
While it can be disheartening to see these violations, there's a silver lining. For all of the top 10 most cited health and safety standards, the total number of violations has decreased from last year’s report. This decline leads us to wonder: Is the drop in violations because we're doing a better job with compliance, or is it because OSHA conducted fewer inspections due to budget constraints and rising costs? Personally, I'm optimistic. I like to think that we are indeed doing a better job in ensuring workplace safety 😊.
For companies looking to improve their safety programs, this report offers a valuable roadmap. By examining the most common violations, organizations can pinpoint weaknesses in their current practices, proactively address risks, and help prevent both OSHA citations and on-the-job injuries. Regular audits, targeted employee training, and a focus on strict compliance with OSHA standards all play key roles in strengthening workplace safety. Additionally, using health and safety software can make a real difference by providing live data, tracking compliance automatically, and making sure corrective actions don’t fall through the cracks.
How SEA Can Help
Safety & Environmental Associates, Inc. (SEA) is dedicated to helping you identify and close gaps in your safety processes. Here’s how we can support you:
Safety Audits & Gap Analysis
We thoroughly evaluate your existing programs, identifying potential hazards and compliance shortfalls before they become costly issues.
Customized Training Programs
From on-site instructor-led training to online and self-paced courses, we tailor our programs to fit your specific workforce and operational needs.
OSHA Compliance & Consultation
Rely on us for up-to-date guidance on OSHA standards and assistance with everything from written safety plans to incident investigations.
Technology Solutions
We can recommend and help implement health and safety software to streamline record-keeping, automate compliance tracking, and provide real-time analytics.
Taking a proactive approach to workplace safety not only protects your team but also reduces legal liabilities and costly fines. Let SEA partner with you to bolster your safety culture and stay ahead of regulatory requirements. Contact us Today!
By Derek Jennings, President SEA
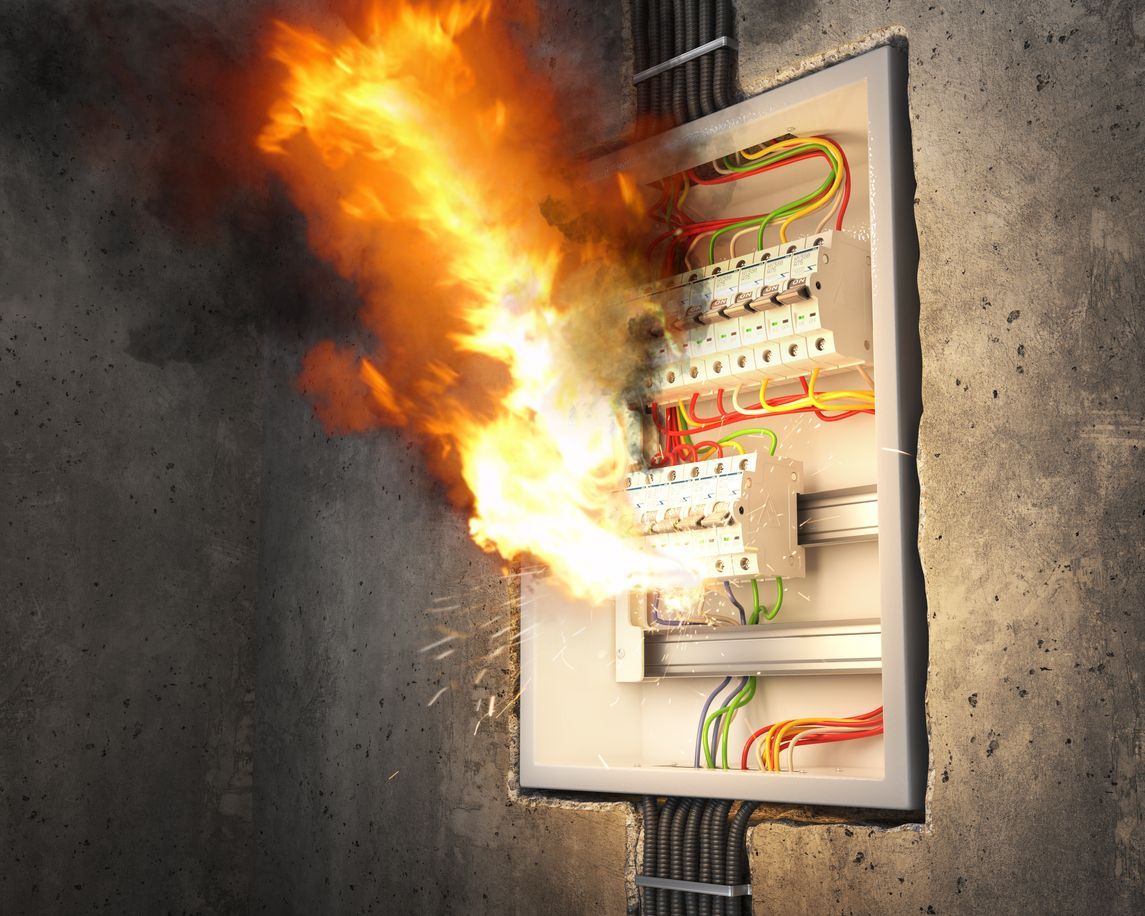