Browse our Blogs
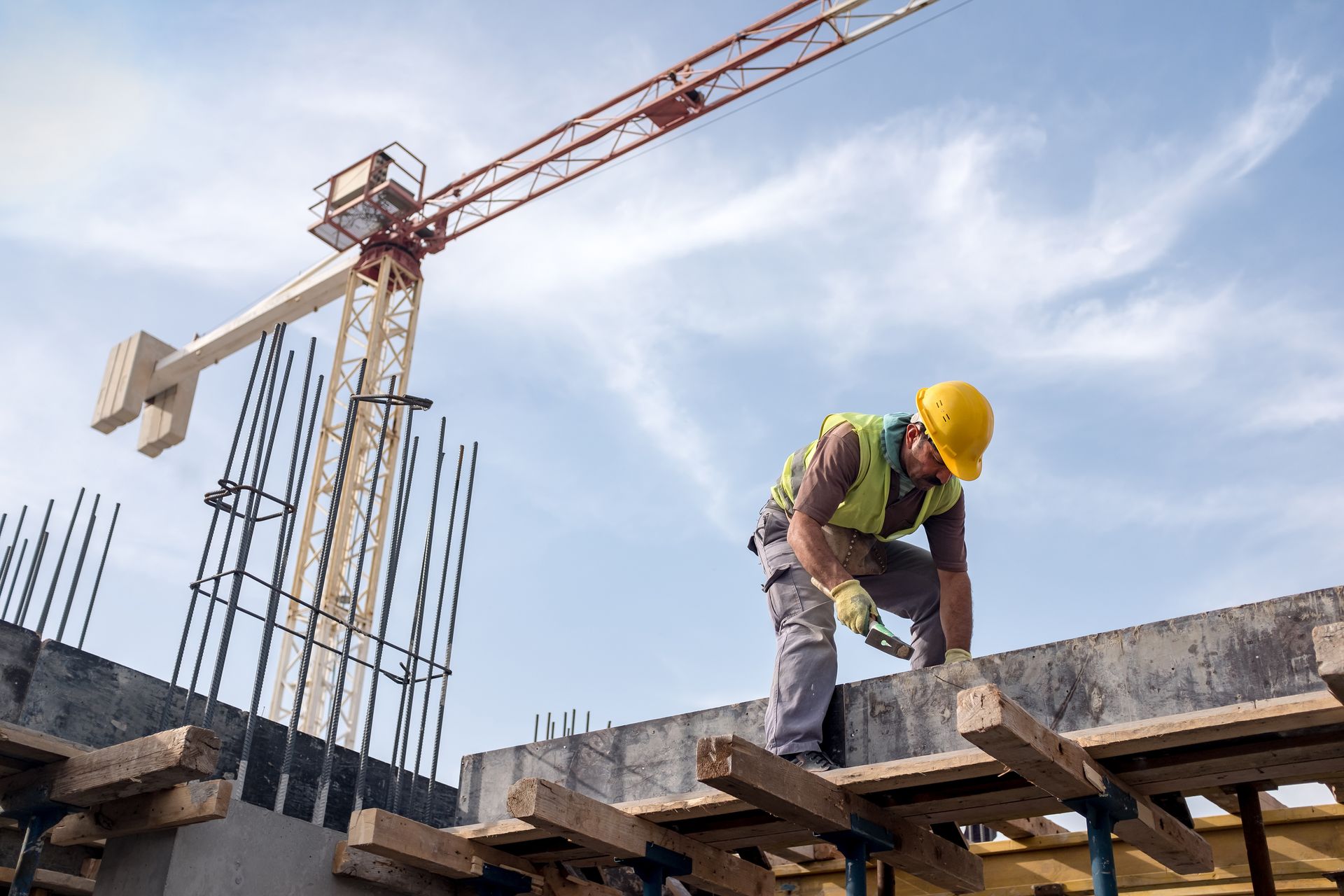
Each year, as the Occupational Safety and Health Administration (OSHA) releases its list of the top 10 workplace safety violations, a pattern emerges that begs a question: Are these frequent violations a sign that employers continue to struggle with the same safety issues, or does it reflect a disposition among OSHA inspectors to focus on areas where they are trained to focus? The Persistent Issue of Repeated Findings The repetition of certain violations year after year might seem surprising, but it underscores a significant challenge in workplace safety management. The top violations tend to be those that are most visible and easiest to spot during inspections, such as fall protection and hazard communication. This consistency suggests that while awareness is high, practical implementation and adherence to safety practices lag behind. Top 10 Most Cited Health and Safety Standards of 2024 1. . Fall Protection, General Requirements: 6,307 violations For the 14th consecutive year, fall protection tops the list of OSHA's enforcement priorities. This emphasis is not arbitrary; OSHA has designated fall protection as a national emphasis area, making it a primary focus during inspections. It's often one of the easiest violations to spot without extensive investigation skills. The OSHA standard 1926.501 mandates that employers must provide fall protection systems like guardrails, safety nets, or personal fall arrest systems for workers at risk of falls of six feet or more in construction and four feet in general industry. Often, the major factor in these violations is human behavior. Many offenders might think, "No one is watching, and this will only take a moment, so it's no big deal." However, this mindset can lead to non-compliance with critical safety measures, putting worker safety at significant risk.
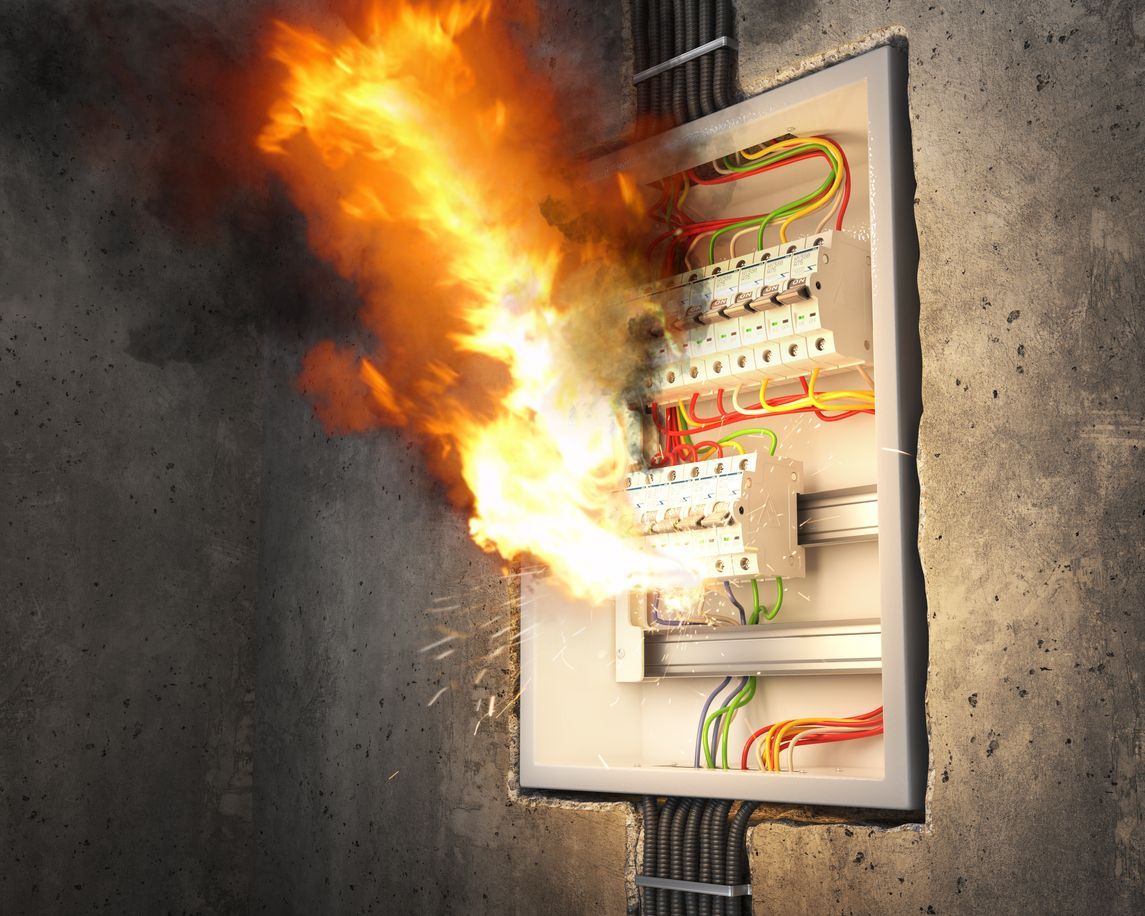
The Occupational Safety and Health Administration (OSHA), in collaboration with the Partnership for Electrical Safety and KEMA Laboratories, has recently unveiled new guidance aimed at addressing arc flash hazards in the workplace. This guidance is a crucial update that highlights the need for comprehensive electrical safety programs that specifically include measures to protect against arc flash hazards. Here’s what employers need to understand about the new directives and how they can effectively respond. Understanding Arc Flash and OSHA's Recommendations An arc flash is a type of electrical explosion that results from a low-impedance connection to the ground or another voltage phase in an electrical system. The new guidance provided by OSHA not only offers a clear definition of what constitutes an arc flash but also elaborates on methods to mitigate such hazards during electrical work. The guidance includes detailed documents for employers and useful handouts for employees, emphasizing the common myths and the reality of arc flash dangers. The Role of NFPA 70E OSHA’s guidance strongly correlates with the standards outlined in NFPA 70E, the National Fire Protection Association’s standard for electrical safety in the workplace. Employers who are already compliant with NFPA 70E likely have a written Electrical Safety Program (ESP) that includes protocols for arc flash hazards. This new guidance serves to reinforce the importance of these existing standards while also urging those without comprehensive plans to take immediate action. What if You Don’t Have a Comprehensive ESP? For employers who have yet to develop an ESP that addresses arc flash hazards, OSHA’s guidance is a wake-up call. It is crucial to recognize that general workplace safety standards, although not specifying arc flash, require protection against electrical hazards under regulations like 1910.333. The absence of specific OSHA standards for arc flash does not excuse employers from the responsibility of protecting their employees from such risks. Implementing Effective Arc Flash Protection Measures Incident Energy Analysis: A foundational step in arc flash protection is conducting an incident energy analysis. This process involves studying the facility’s electrical systems to calculate the potential energy released in the event of an arc flash. Understanding this energy potential is essential for determining the arc flash boundary—the distance within which a person could receive second-degree burns or worse if exposed to an arc flash. Developing a Risk Assessment Procedure: Employ ers need to establish a procedure for assessing the risks associated with arc flash. This includes evaluating the tasks being performed, the condition of the electrical equipment, the maintenance history of the equipment, the energy involved, and the potentia l for human error. Deciding on Protective Measures: Once risks are assessed, decisions must be made regarding the best ways to protect employees. This often involves the use of Arc-Rated Pe rsonal Protective Equipment (PPE) and could also include engineering controls such as redesigning parts of the electrical system to minimize arc flash risks. Proactive Versus Reactive: The Choice is Yours The latest guidance from OSHA should be viewed as an unofficial yet critical call to action for employers to either update their existing safety measures or develop new protocols in line with NFPA 70E. Being proactive about electrical safety not only helps in compliance with OSHA’s standards but fundamentally enhances the safety and well-being of employees. Final Thoughts The introduction of OSHA’s arc flash guidance is a significant step toward heightened awareness and improved safety practices surrounding electrical hazards in the workplace. Employers are encouraged to review their current safety protocols, educate their workforce about the dangers of arc flash, and implement comprehensive measures to prevent such incidents. Always keep in mind that workplace safety begins with staying informed and well-prepared. Make it a habit to test before you touch it and prioritize safety like your life depended on it! For more insights into workplace safety and compliance, keep following our blog. Your safety is our priority, and together, we can foster a safer working environment for all. By Derek Jennings President SEA

As wildfires continue to blaze across regions like Los Angeles, CA, they leave behind more than just scorched earth. The air quality in affected and surrounding areas deteriorates significantly, posing severe health risks to residents. Understanding the transformation of plant materials into char and ash during these fires, and the subsequent impact on our environment and health, is crucial for community safety and preparedness. The Science Behind the Smoke: Pyrolysis and Wildfires When wildfires burn through vegetation, the intense heat triggers a chemical process known as pyrolysis. This is where organic materials (like plants) break down under high temperatures in the absence of oxygen, transforming into various gases and liquids, and a solid residue rich in carbon, known as char. As the fire consumes more material, the process continues, leaving behind a substantial amount of ash, which consists mainly of inorganic substances. Both char and ash are significant byproducts of wildfires and contribute to the complex makeup of wildfire smoke. The Dangers of Char and Ash Air Quality Degradation: The small particles of char and ash produced during wildfires can become airborne and are small enough to be inhaled deeply into the lungs. They can travel vast distances, affecting air quality over broad areas. This particulate matter (PM) can penetrate indoor environments, making virtually no place safe from its reach. Health Implications: The health risks associated with poor air quality during and after a wildfire are significant. Inhalation of fine particulate matter from char and ash can lead to respiratory issues such as asthma attacks, bronchitis, and other chronic respiratory conditions. It can also exacerbate heart conditions, leading to increased hospital visits, and in severe cases, premature death. Vulnerable populations, including children, the elderly, and those with preexisting health conditions, are particularly at risk. Environmental Impact: Beyond human health, the environmental impact of char and ash is profound. These substances can contaminate water sources and soils, leading to long-term ecological damage and affecting the regrowth and recovery of natural habitats. Combustion Product Analysis: A Critical Need In the aftermath of a wildfire, analyzing the combustion products —char and ash—is essential to assess the environmental and health impact comprehensively. This analysis helps in understanding the specific contaminants released and assists in formulating strategies for cleanup and mitigation to prevent further harm to public health and the environment. Precautions and Recommendations Stay Informed: Keep track of air quality indexes (AQI) in your area through reliable sources to know when the air is unsafe. Limit Exposure: Avoid outdoor activities during high AQI levels. Keep windows and doors closed to minimize indoor air pollution. Use Air Purifiers: High-efficiency particulate air (HEPA) purifiers can help reduce indoor air particulate levels. Consult Health Professionals: If you experience any health issues related to air quality, consult medical professionals immediately. As communities near and far from the immediate blaze cope with the fallout of these devastating fires, understanding the complexities of wildfire smoke, specifically the roles of char and ash, becomes paramount. By staying informed and prepared, individuals and communities can better protect themselves from the less visible, but equally dangerous, aspects of wildfires. By Derek Jennings, President SEA
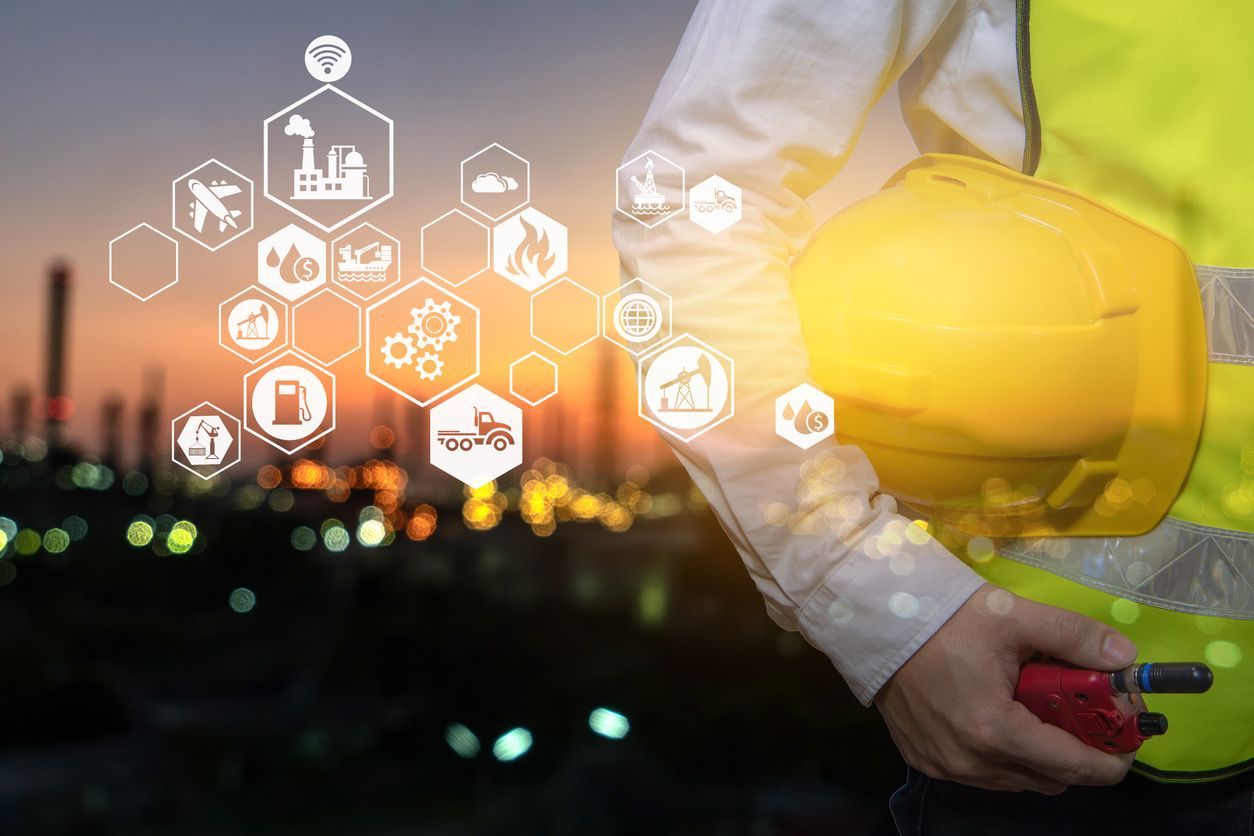
Hello everyone, and Happy New Year! I wanted to take a moment to apologize for the quiet spell on our blog over the last few months. The final quarter of the year was exceptionally busy for us at SEA, and although it's been a whirlwind of activity, it meant that I couldn't dedicate as much time to our blog as I would have liked. I've received your emails and messages letting me know I was missed, and I can't tell you how much that means to me! Thank you for sticking around and for your thoughtful notes. I'm excited to say that we're back on track now, and I promise to keep bringing you more informative and engaging content. Here is the first of many so Stay tuned! Since it is Injury and Illness Reporting time let's take a look at 2023. The Occupational Safety and Health Administration (OSHA) has recently released comprehensive data for workplace injuries and illnesses recorded in 2023, providing key insights that can help businesses enhance their safety protocols and reduce the risk of incidents. This annual release plays a crucial role in helping organizations assess the effectiveness of their safety measures and implement necessary improvements. Key Findings from OSHA’s 2023 Data OSHA’s report details various statistics related to workplace injuries and illnesses, highlighting trends and areas that need attention. The data reveals that while some industries have seen improvements in safety measures, others continue to face challenges in reducing the number of incidents. The agency uses this data to inform policy decisions, guide inspections, and provide targeted assistance to industries with higher rates of incidents. Trends and Statistics The report categorizes data according to different industries, types of injuries, and causes. This segmentation helps organizations identify specific risk factors prevalent in their operations and benchmark their safety performance against industry standards. The Importance of Accurate Injury and Illness Reporting Accurate reporting of workplace injuries and illnesses is not just a regulatory requirement—it is a critical component of an effective safety and health management system. Proper documentation helps identify hazard patterns and can be a basis for introducing preventive measures. It also ensures that workers receive appropriate medical care and compensation for work-related injuries or illnesses. How Businesses Can Improve Reporting Practices Training : Ensure that staff responsible for reporting are welltrained on OSHA’s requirements. Regular training sessions can help keep everyone updated on the latest regulations and reporting procedures. Clear Procedures: Establish clear and straightforward procedures for reporting injuries and illnesses. This includes defining who is responsible for reporting and the steps they need to follow when an incident occurs. Encourage Reporting: Create a workplace culture that encourages prompt and accurate reporting of injuries and illnesses. Workers should feel safe and supported in reporting, without fear of retaliation. SEA’s Role in Enhancing Workplace Safety At Safety & Environmental Associates, Inc. (SEA), we understand the challenges businesses face in maintaining a safe workplace and complying with regulatory requirements. We offer a range of services designed to improve injury and illness reporting practices and overall safety management: Safety Audits and Consultations: Our experts can help you assess your current safety protocols and identify areas for improvement. Customized Training Programs: We provide training tailored to the needs of your staff and the specifics of your industry, focusing on both compliance and practical safety management. Ongoing Support: SEA offers continuous support to help businesses implement long-term safety solutions that can adapt to changing regulations and business needs. Conclusion The release of OSHA’s 2023 injury and illness data serves as a reminder of the ongoing need for vigilance and continuous improvement in workplace safety. By understanding and utilizing this data, businesses can better protect their employees and enhance their compliance with safety regulations. For assistance with interpreting OSHA data, improving your reporting processes, or enhancing your overall safety management practices, reach out to Safety & Environmental Associates, Inc. today. Let us help you build a safer and more compliant workplace. By Derek Jennings, President SEA
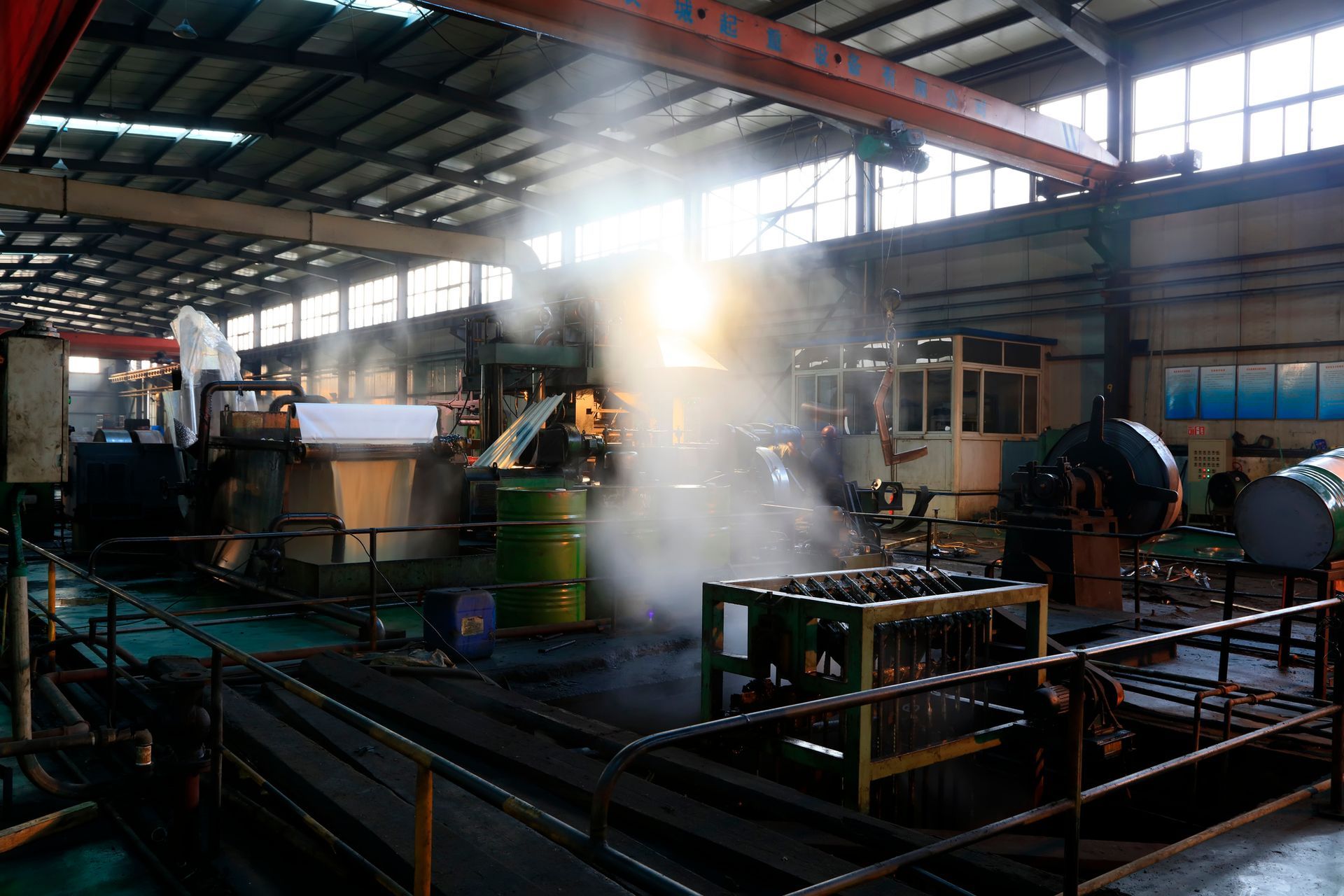
Last month, the Environmental Protection Agency (EPA) introduced a pivotal update to its air quality standards by lowering the allowable concentration of fine particulate matter (PM2.5) from 12 µg/m³ to 9 µg/m³. This revision, the first in over a decade, signals a crucial step forward in the nation’s efforts to enhance public health protections against the smallest and most dangerous airborne pollutants. Understanding PM2.5 and Its Impact Particulate matter 2.5 (PM2.5) consists of fine particles with diameters that are 2.5 micrometers and smaller. These particles are particularly hazardous as they can penetrate deep into the lungs and even enter the bloodstream, causing a variety of health problems—from acute respiratory symptoms to chronic diseases like asthma, heart disease, and others. The urgency to control PM2.5 emissions is not just about compliance; it’s about protecting lives. Why the Stricter Standards? Research continually supports that lower concentrations of PM2.5 are associated with improved cardiovascular and respiratory health outcomes in communities. By tightening the standards, the EPA aims to prevent more of these health issues, particularly in vulnerable populations such as children, the elderly, and those with preexisting conditions. How SEA Helps Industries Adapt to New Regulations At Safety & Environmental Associates, Inc. (SEA), we specialize in providing comprehensive air quality monitoring and compliance solutions that help businesses meet stringent environmental standards. Here’s how we can assist in light of the new PM2.5 regulations: Cutting-Edge Monitoring Technologies - SEA employs advanced monitoring technologies that can detect and quantify PM2.5 levels with precision. These technologies are critical for providing accurate, real-time data that businesses need to ensure they remain within the new regulatory limits. Expert Compliance Strategy Development - Our environmental specialists provide more than just testing; they help businesses develop and implement effective compliance strategies. This includes performing risk assessments, suggesting mitigation techniques, and optimizing operational practices to reduce particulate emissions. Regular Testing and Documentation - SEA conducts regular environmental testing to track compliance with EPA standards. Our thorough documentation helps businesses provide evidence of compliance during inspections and reviews, ensuring transparency and accountability. Technical Insights and EPA Resources For those interested in a deeper dive into the technical aspects of PM2.5 monitoring and compliance, the EPA provides extensive resources. These include guidelines on measurement methods, health impact studies, and detailed descriptions of regulatory requirements. Businesses can access these resources to better understand the expectations and methodologies recommended by the EPA. EPA PM2.5 Overview and Health Impacts National Ambient Air Quality Standards (NAAQS) for PM Technical and Regulatory Information on PM2.5 Partner with SEA for PM2.5 Compliance Adhering to the new PM2.5 standard is essential not just for regulatory compliance but for the health and safety of all. SEA is ready to help your business navigate these changes effectively, ensuring that you meet or exceed the new standards with our expert testing and environmental services. To learn more about how SEA can assist your company in achieving and maintaining compliance with the latest EPA air quality standards, please contact us today. Let’s work together to make our air cleaner and our communities healthier. By Derek Jennings, President SEA
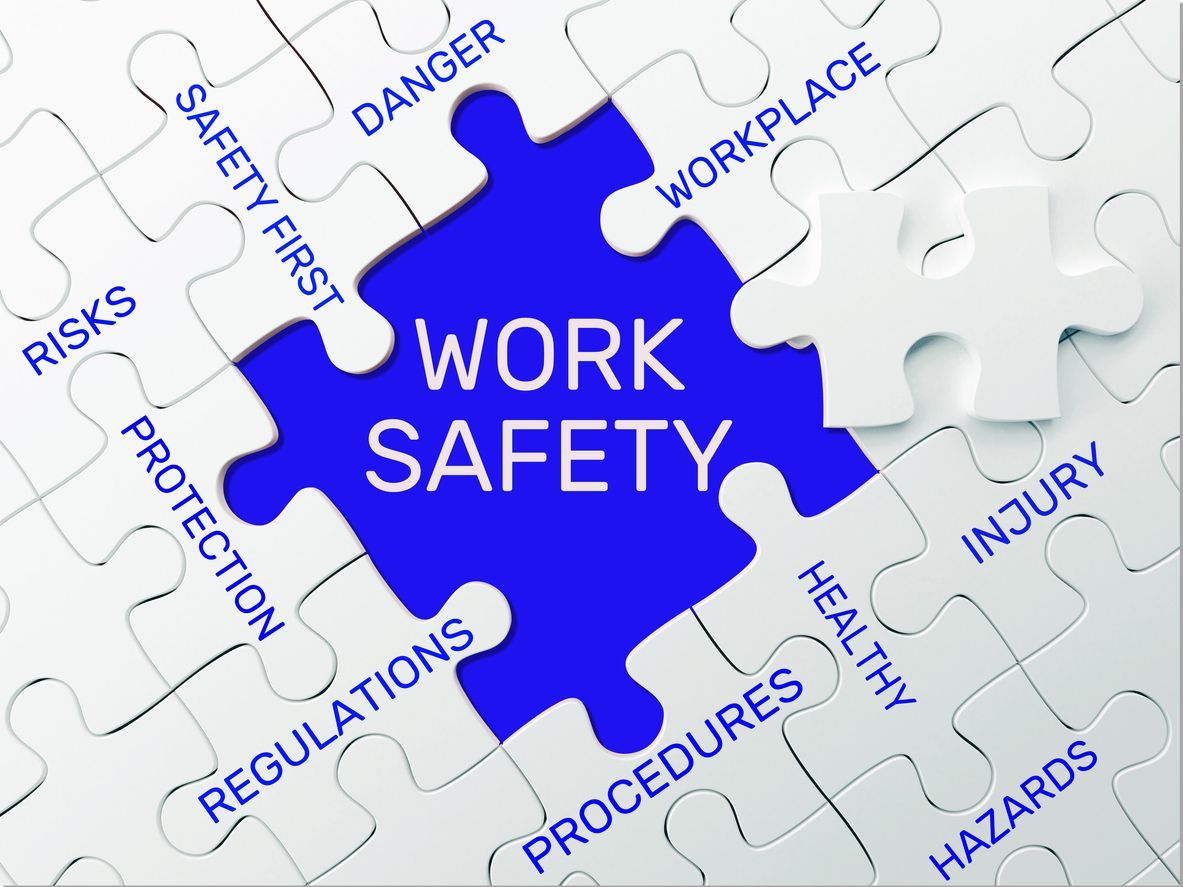
As safety professionals, keeping up with regulatory updates is essential to ensuring a safe and compliant workplace. The Occupational Safety and Health Administration (OSHA) has made significant updates to the Hazard Communication Standard (HazCom), which aim to improve safety across industries that handle chemicals. These changes reflect a global move towards better hazard communication and are designed to reduce workplace incidents by providing clearer, more accessible information. Here’s a deeper dive into what these updates entail and how you can effectively implement them in your workplace. What is getting updated? More Detailed Hazard Classification OSHA's update includes a more detailed framework for classifying the health and physical hazards of chemicals. This enhancement aligns more closely with the Globally Harmonized System (GHS) and aims to provide uniformity in hazard assessment. What this means for your workplace is that every chemical can now be assessed with a clearer set of criteria, reducing variability and enhancing the accuracy of hazard identification. Comprehensive Labeling Enhancements The revisions to labeling requirements are substantial. The new labels will now feature: Updated Pictograms: Clearer visual symbols that quickly communicate specific hazard information Enhanced Hazard Statements: Specific phrases describing the nature and degree of hazard a chemical presents. Precautionary Statements : Di rections on how to minimize or prevent adverse effects from exposure. Signal Words: "Danger" or "Warning" to emphasize the severity of the hazard. These changes are designed to provide instant recognition and understanding, making it quicker and easier for workers to respond appropriately to potential hazards. Standardized Safety Data Sheets The standardization of Safety Data Sheets into a consistent 16- section format is a key update. This structure ensures that information such as chemical properties, instructions for safe handling, and emergency control measures are uniformly presented, which is crucial during emergency responses. The sections are organized to facilitate quick access to information that is most likely needed in an emergency. Steps to Implement the Updated HazCom Standard Review and Update Your Chemical Inventory Begin by auditing your current chemical inventory. Ensure every chemical has an updated Safety Data Sheet and that all labels reflect the new standards. This may require coordination with chemical suppliers to obtain the most current information. Educate and Train Your Workforce Update your training programs to include the new labeling elements and the format of the SDSs. Training should be comprehensive and include practical exercises that help employees familiarize themselves with interpreting the new information. Consider regular refreshers to ensure ongoing compliance and safety . Revise and Distribute Updated Safety Materials Once you've updated the SDSs and labels, distribute these materials to all relevant areas of your operation. Make sure that all employees know where to find these documents and understand how to use them in their daily operations and in emergency situations. Monitor and Audit for Compliance Regularly auditing your processes and pr actices is crucial to ensure ongoing compliance. This includes periodic checks of chemical storage areas, random reviews of SDSs and labels, and assessments of employee knowledge through quizzes or informal discussions. How SEA Can Support Your Transition At Safety & Environmental Associates, Inc. (SEA), we specialize in helping companies like yours navigate complex regulatory landscapes. We offer tailored support in auditing your current hazard communication programs, developing and delivering targeted training, and ensuring that your documentation and labeling are up to date. Embrace these changes with confidence by partnering with SEA. Let us help you enhance your workplace safety standards while ensuring full compliance with OSHA’s updated HazCom rules. Reach out today to start the conversation about how we can support your safety goals. By Derek Jennings, President SEA
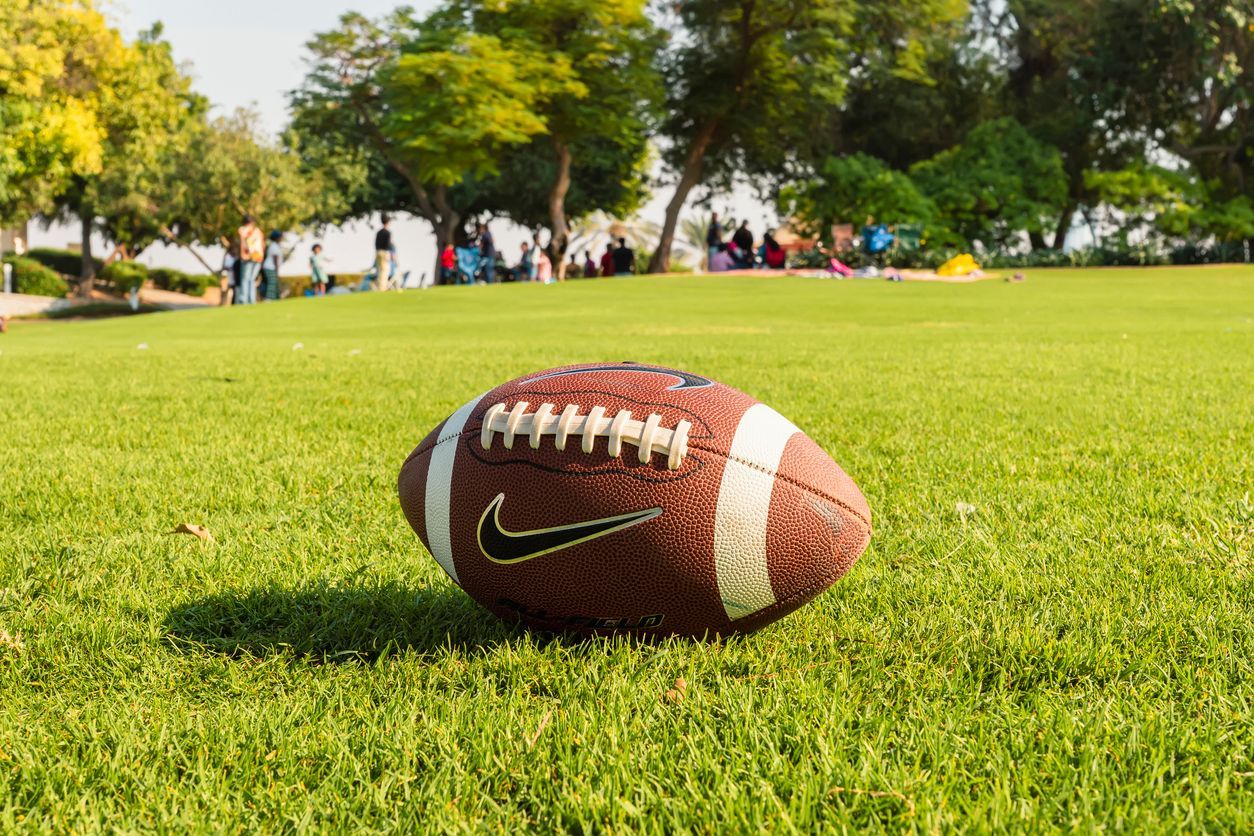
In the realm of professional sports, particularly in the National Football League (NFL), player safety, especially regarding head injuries, has been a significant concern for years. Recent developments, as highlighted in an insightful article from ISHN's September 2024 issue, underscore the complexities and advancements in managing these risks. The NFL's adoption of the Guardian Cap illustrates a proactive approach to enhancing player safety, a move that echoes broader safety management principles applicable across various industries. The Challenge of Head Injuries in the NFL Head injuries, including concussions, have been a longstanding issue in the NFL, with players experiencing higher rates of Alzheimer's, ALS, Parkinson's, and dementia compared to the general population. In 2023 alone, there were 219 reported concussions, a figure that, while below the peak of previous years, remains alarming. This persistent risk has spurred the NFL to seek innovative solutions to protect players without compromising their performance. Introducing the Guardian Cap One significant advancement is the introduction of the Guardian Cap, a soft, padded outer shell worn over the standard helmet during practices. This cap provides an additional layer of protection, potentially reducing the impact force experienced during collisions. Initially adopted in practice settings, the Guardian Cap has been mandatory for certain player positions during preseason and regular-season practices, reflecting a strategic approach to integrating new safety equipment. Player Resistance and the Swag Factor Despite the safety benefits, the adoption of the Guardian Cap has not been without resistance. Players have expressed concerns about the aesthetics of the additional gear, indicating a preference for maintaining a certain image, or "swag," which is perceived to be compromised by the bulky appearance of the cap. This resistance is emblematic of broader challenges faced by safety professionals across sectors, where personal preferences and workplace culture often influence compliance with safety measures. Lessons for Broader Safety Management The situation in the NFL serves as a compelling case study for safety managers in various industries. It highlights the need for: Engagement and Education: Just as NFL teams must communicate the importance of safety gear, employers should engage with employees to educate them about the risks and the protective measures in place. Cultural Integration: Integrating safety measures into the existing workplace culture, much like integrating safety gear into players’ gear, can help in reducing resistance. Innovative Solutions: Ju st as the NFL explored new technologies like the Guardian Cap, industries should invest in innovative solutions that enhance safety without significantly impacting workflow or employee comfort. Conclusion: SEA's Role in Enhancing Your Safety Strategies At Safety & Environmental Associates, Inc. (SEA), we understand the challenges of implementing effective safety measures that balance protection with practicality and employee acceptance. Drawing on lessons from fields as diverse as professional sports, we are equipped to help you develop safety strategies that not only comply with regulations but are also embraced by your team. Interested in enhancing your workplace safety protocols? Contact SEA today to learn how we can assist you in developing and implementing safety solutions that protect your employees and your bottom line.
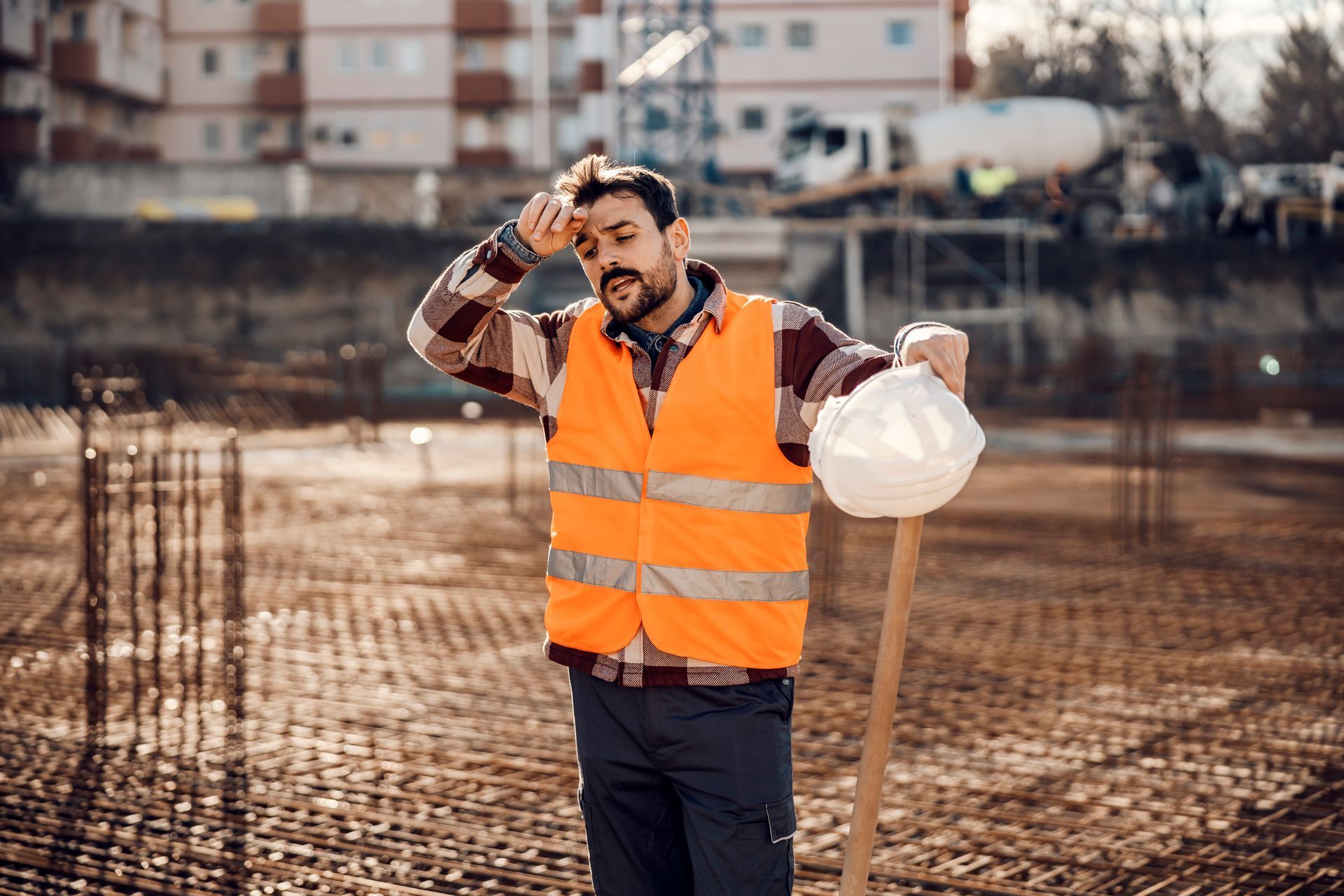
The American Industrial Hygiene Association (AIHA) has recently unveiled a groundbreaking tool that promises to significantly improve how businesses manage heat stress in the workplace. The new app is designed to help safety professionals monitor and manage heat stress more effectively, ensuring a safer work environment for all employees. Understanding the AIHA Heat Stress App This innovative app allows users to input various environmental factors such as temperature, humidity, and solar radiation to receive real-time assessments of heat stress conditions. By using this app, safety managers can quickly determine when the conditions are becoming hazardous and implement preventative measures to protect workers. Key Features and Benefits Real-Time Data: The app provides instant feedback on the heat index at the workplace, allowing for timely decisions and interventions. Customizable Alerts: Users can set up alerts for specific conditions, ensuring that they are immediately informed about potential heat stress risks. Historical Data Analysis: The app records data over time, which can be analyzed to understand and mitigate recurring heat stress issues The Importance of Managing Heat Stress Heat stress can lead to serious health issues such as heat exhaustion, heat stroke, and even death. It is particularly concerning in industries like construction, manufacturing, and agriculture where employees are often exposed to high temperatures for extended periods. The AIHA app is a vital tool in combating these risks by providing essential information that can prevent heat-related illnesses. Implementing the App in Your Safety Strategy Incorporating the AIHA Heat Stress App into your workplace safety strategy can significantly enhance your ability to manage and mitigate heat stress. It serves as an essential component of a comprehensive safety plan, providing critical information that can be used to adjust work practices, schedules, and safety measures according to real-time conditions. How SEA Can Help At Safety & Environmental Associates, Inc. (SEA), we understand the challenges businesses face in managing workplace hazards such as heat stress. Our team of experts can assist you in integrating the AIHA Heat Stress App into your existing safety protocols and provide ongoing support in optimizing its use for maximum safety. Conclusion: Take Action to Protect Your Workforce With rising global temperatures, managing heat stress is more critical than ever. The AIHA Heat Stress App is an excellent resource for any business committed to maintaining a safe working environment. Contact SEA today to learn more about how this tool can be part of your safety solutions and to discuss other ways we can help you keep your workforce safe and healthy By Derek Jennings, President SEA