Ensuring Employee Accountability
Ensuring Employee Accountability: A Call for Citing Employees Under OSHA's General Duty Clause
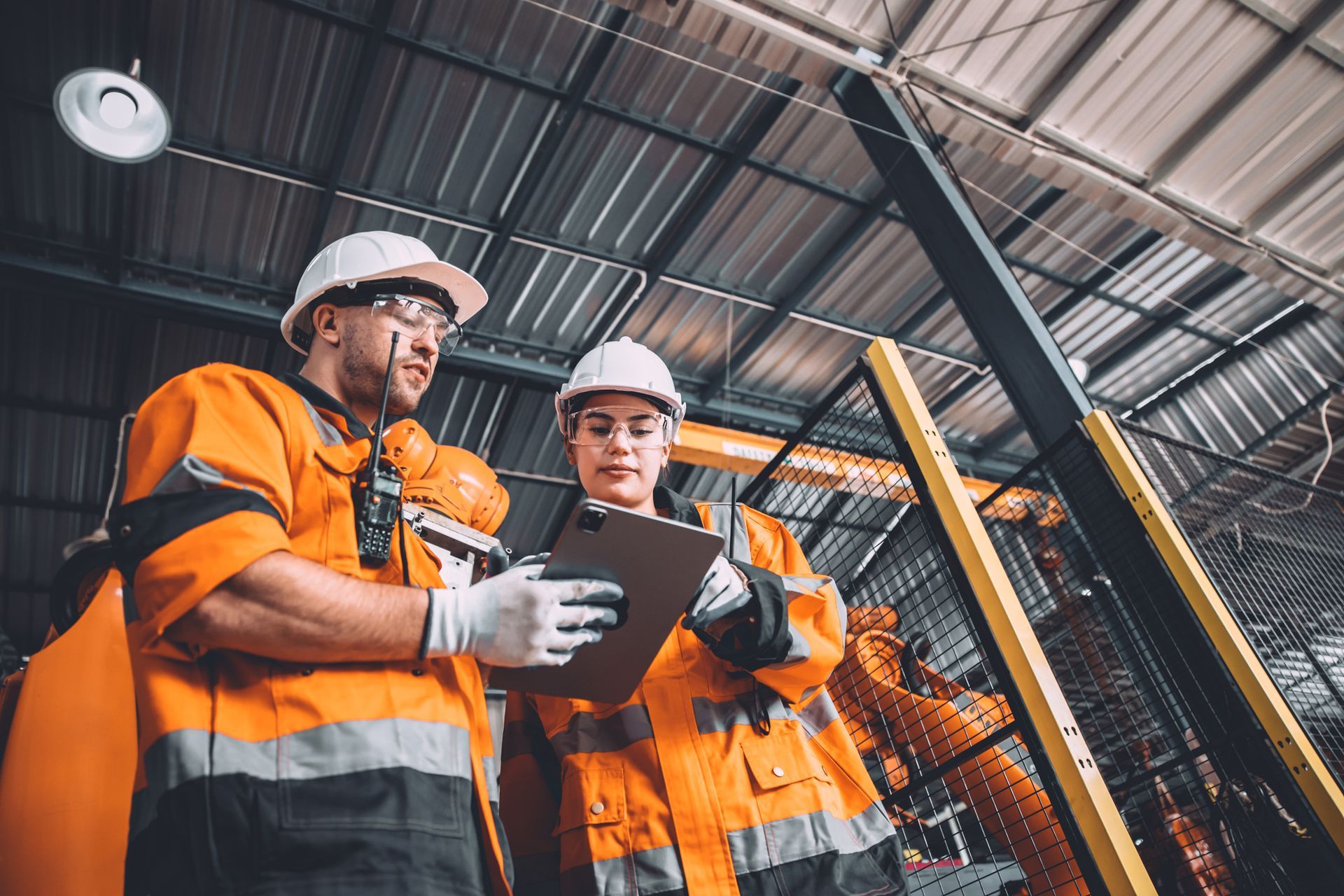
The principles of workplace safety and health have primarily been focused on employer responsibilities, as they are primarily the ones shaping work conditions. Yet, as we further delve into the complexities of occupational safety, it becomes increasingly apparent that employees play a crucial role. While employers must certainly continue their efforts to foster safe work environments, it is also vital that employees be held accountable for their actions regarding safety, and this can be done by citing OSHA's General Duty Clause, Section 5(b).
The Occupational Safety and Health Act's General Duty Clause, Section 5(b) states that each employee must comply with occupational safety and health standards. This includes all rules, regulations, and orders issued under the Act, which apply to their actions and conduct. Traditionally, enforcement of this clause has been indirect, with employers bearing the brunt of penalties for employee non-compliance. However, a more direct approach could have a profound impact on overall workplace safety.
With this in mind, it is essential to discuss the Employee Misconduct Defense, a tool that employers can use to reduce OSHA fines. This defense comprises four elements: 1) written safety rules, policies, and procedures; 2) adequate safety training; 3) self-inspection and auditing; and 4) documented discipline for safety infractions.
By having clear, written safety rules, policies, and procedures, employers lay a foundation of expectations for employee behavior. Training is the next essential step; it empowers employees with the knowledge and skills necessary to adhere to safety standards and rules. Furthermore, self-inspection and auditing mechanisms allow employers to ensure consistent adherence to these rules and identify areas for improvement. Lastly, a documented discipline system provides a clear record of steps taken to address employee misconduct, proving the employer's proactive stance towards safety.
Employers often find it challenging to fulfill all these elements. However, doing so not only strengthens their defense against potential OSHA penalties but also enhances their safety culture. If every employer embraces this rigorous approach, employees would be well-equipped with the necessary knowledge and be aware of the consequences of their actions.
Studies have shown that a high percentage of workplace accidents are due to human error, often resulting from negligence or non-compliance with safety protocols. According to the National Safety Council, 85% to 98% of all workplace accidents are caused by employee mistakes, whether due to carelessness, fatigue, or disregard for safety rules. Despite the measures employers put in place to minimize these hazards, the implementation of safety procedures is largely dependent on the actions of the employees themselves.
Citing employees under Section 5(b) is not a call for punishment or fines, but rather a mechanism to bolster personal responsibility and heighten awareness of safety standards. The objective is not to penalize but to provide constructive feedback that will foster an ingrained culture of safety in the workplace. An understanding of accountability would act as an additional deterrent to negligence and create a more safety-conscious employee base.
The introduction of this practice would also lead to statistical improvements in safety outcomes. With employee errors contributing to 98% of accidents, even a conservative estimate of a 10% improvement in employee compliance due to increased accountability could lead to a significant 9% overall reduction in accidents. This shift could save thousands of lives and prevent countless injuries, considering that, according to the Bureau of Labor Statistics, there were 2.8 million nonfatal workplace injuries and illnesses reported in the United States in 2019 alone.
Moreover, it is not just about reducing accident numbers. A safer workplace results in improved morale, increased productivity, and lower absenteeism. It becomes a virtuous cycle that fosters a healthier, more productive work environment for everyone.
Therefore, it is in the best interest of all parties involved to consider this proposition. A citation under Section 5(b) could serve as a wake-up call for an employee to reassess their approach to safety. Employers gain a safer, more productive workforce, and society as a whole benefits from a reduction in the number of workplace accidents and fatalities. By holding every member of the workforce accountable for maintaining a safe and healthy workplace, we can create a culture that truly values safety and continually works toward its betterment.
Derek Jennings,
President Safety & Environmental Associates, Inc.
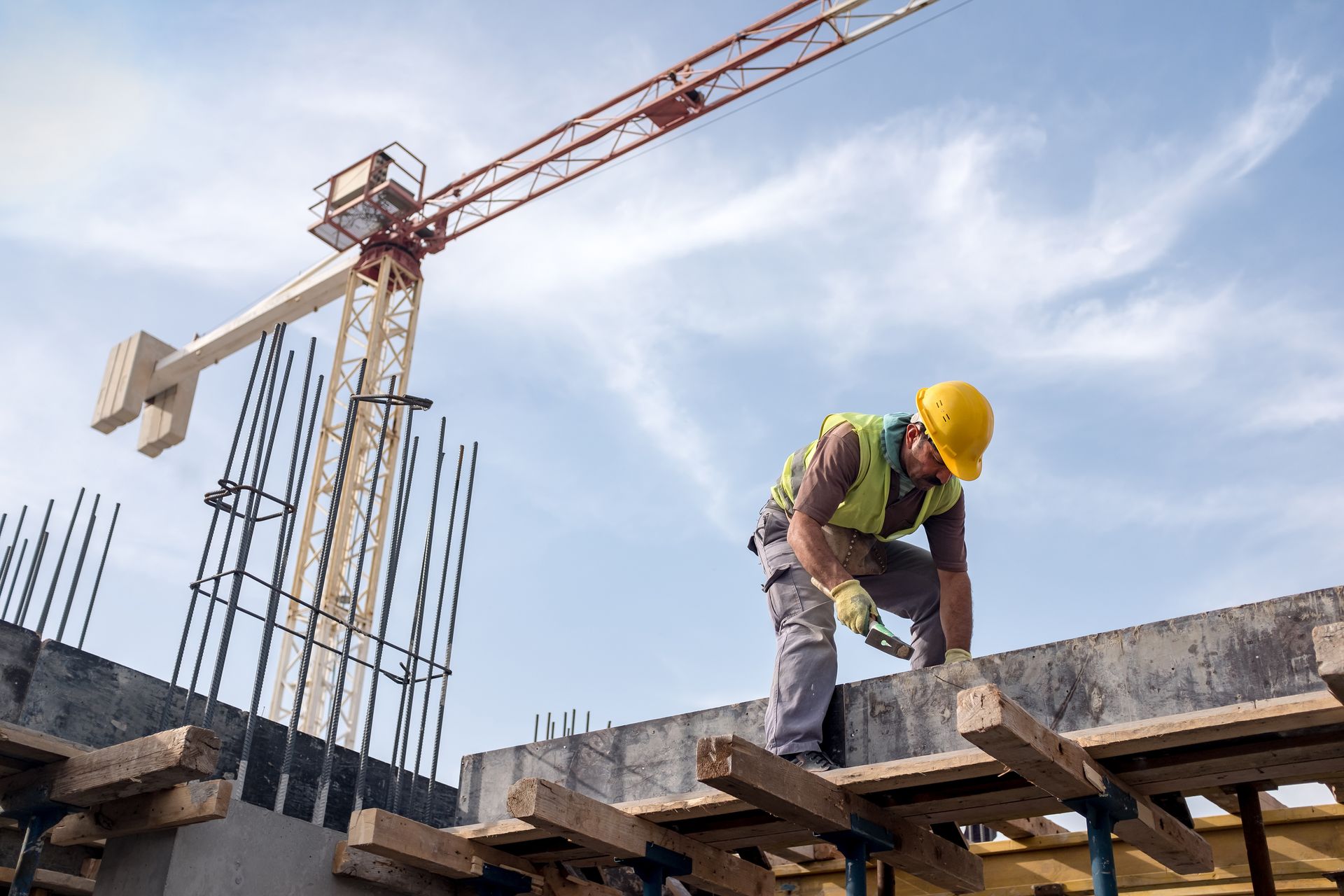
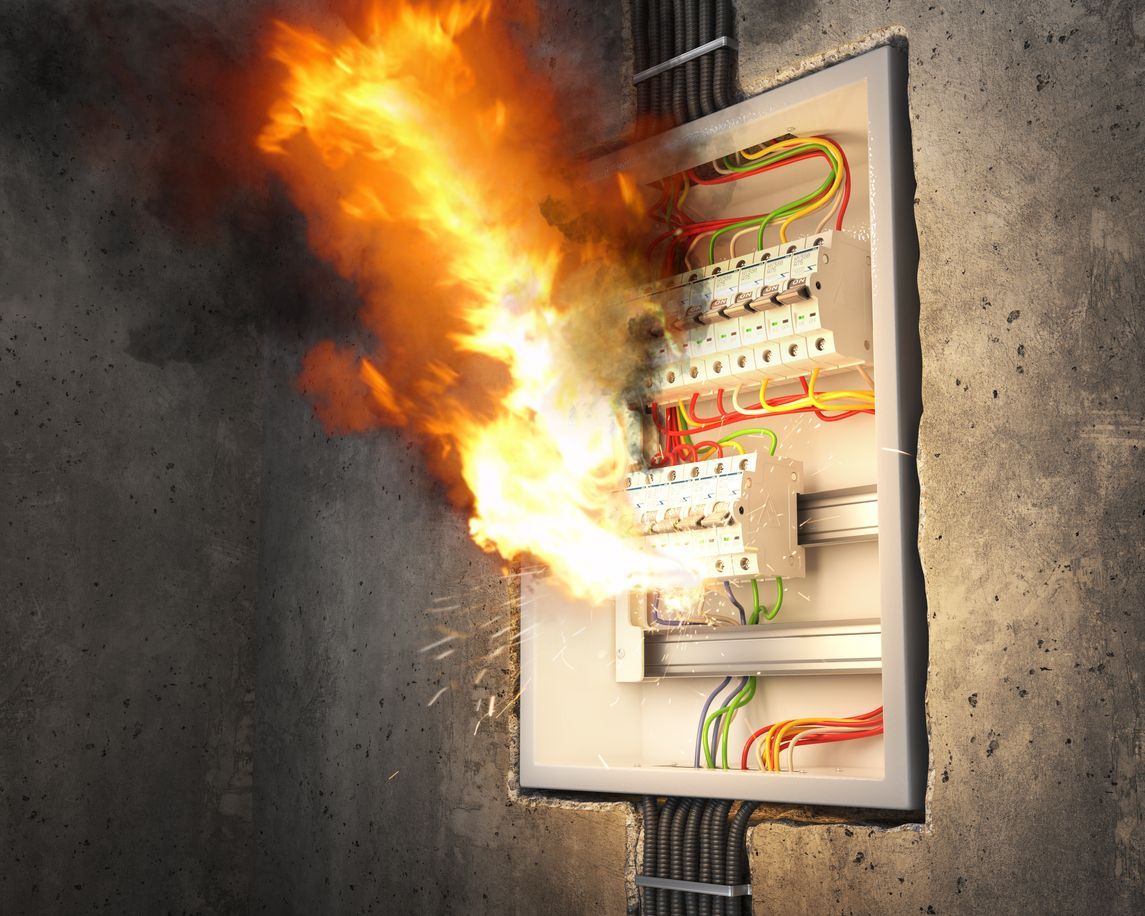