OSHA's Upcoming Heat Rule: What Employers Should Know
Turning Up the Heat on Safety: How OSHA's Upcoming Rule Impacts Your Business and How SEA Can Guide You Through!
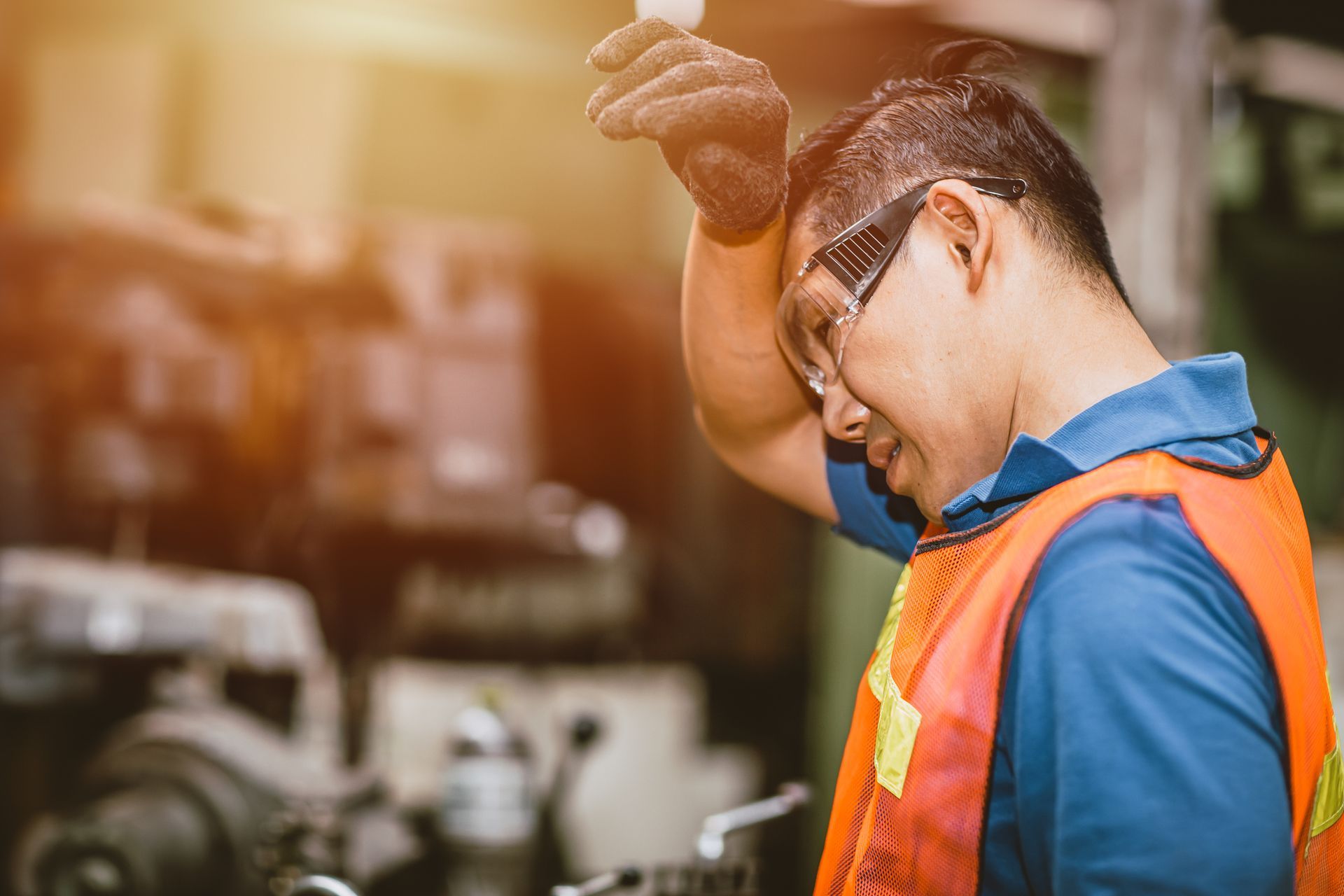
The Occupational Safety and Health Administration (OSHA) is preparing to launch a pivotal regulation that will lay out comprehensive requirements for employers. These rules will detail how businesses should prevent and address heat-related illnesses and injuries in their workforce, regardless of whether the work is indoors or outdoors.
Background:
This advanced rule, originally introduced in 2021, is nearing its final stages. Upon completion, OSHA will invite further public commentary. However, once formalized, legal battles might delay its implementation for an extended period. Interestingly, OSHA is now keen on gathering insights from small businesses, particularly those most likely affected by these standards. One might question why this wasn't a priority earlier. This outreach is part of a mandatory small business impact study. Failing to carry out this study could weaken the rule's legal standing, especially if businesses feel OSHA has overstepped. OSHA has specifically requested feedback from sectors like warehousing, agriculture, construction, manufacturing, oil and gas, waste management, utilities, food service, and landscaping. The rule also awaits White House review. With President Biden previously voicing strong support for OSHA's heat-focused initiative, approval seems likely.
Potential Rule Content:
Union perspectives will undoubtedly shape the rule. For instance, OSHA has been particularly vigilant with Amazon, given the ongoing nationwide union-organizing campaign targeting its distribution centers. OSHA's National Emphasis Program (NEP) has also spotlighted the warehousing industry, pushing for intensified inspections.
The focus is on immediate responses to heat hazard complaints and hospitalizations. The goal is to encourage proactive employer interventions to mitigate heat-related issues.
Despite the prevalent concern about heat-related risks, OSHA had never formalized a regulation addressing this. Enforcement was generally anchored on the General Duties Clause of the OSH Act, which mandates a safe and healthy workplace for employees.
Several companies, including Amazon, have innovated with temperature controls and heat safety protocols. For outdoor workers in construction, road repair, and utilities, battling the summer sun remains a challenge.
Notably, 26 states with OSHA-approved state plans have specific laws on occupational heat exposure. OSHA's new rule might integrate existing state standards and insights from recent enforcement initiatives.
NIOSH's Suggestions:
OSHA has collaborated with the National Institute for Occupational Safety and Health (NIOSH) on the rule's content. NIOSH's recommendations include:
- Using machinery to reduce strenuous manual labor.
- Gradually acclimating workers to heat over a 7 to 14 day period.
- Restricting new workers to 20% of typical hot environment work time initially, increasing 20% daily.
- Promoting regular water intake (a cup every 15-20 minutes).
- Ensuring access to shaded or cooled spaces.
- Keeping an eye on complicating factors like alcohol consumption or low-grade infections.
- Offering cooled clothing or fluids and using reflective attire for those in industrial settings.
Presently, OSHA advises maintaining temperatures between 68◦ F and 78◦ F, providing water and breaks, and preparing workers for the heat. OSHA has also curated a detailed guide to help businesses prevent heat illnesses.
Employers are advised to familiarize themselves with these guidelines, ensuring safety and preparation for any OSHA evaluations or the eventual implementation of the new rule.
How SEA can Help!
As we navigate the evolving landscape of heat-related safety standards, SEA stands at the forefront of ensuring a seamless transition for businesses. Our expertise extends beyond mere compliance. We understand the nuances of diverse work environments and can provide tailored solutions that prioritize both employee welfare and operational efficiency. By partnering with SEA, employers can be assured of a proactive approach to heat-related challenges, harnessing cutting-edge technologies, training programs, and best practices. Let SEA be your compass in guiding your business towards a safe, productive, and heat-resilient future.
By Derek Jennings, President Safety & Environmental Associates (SEA) Inc.
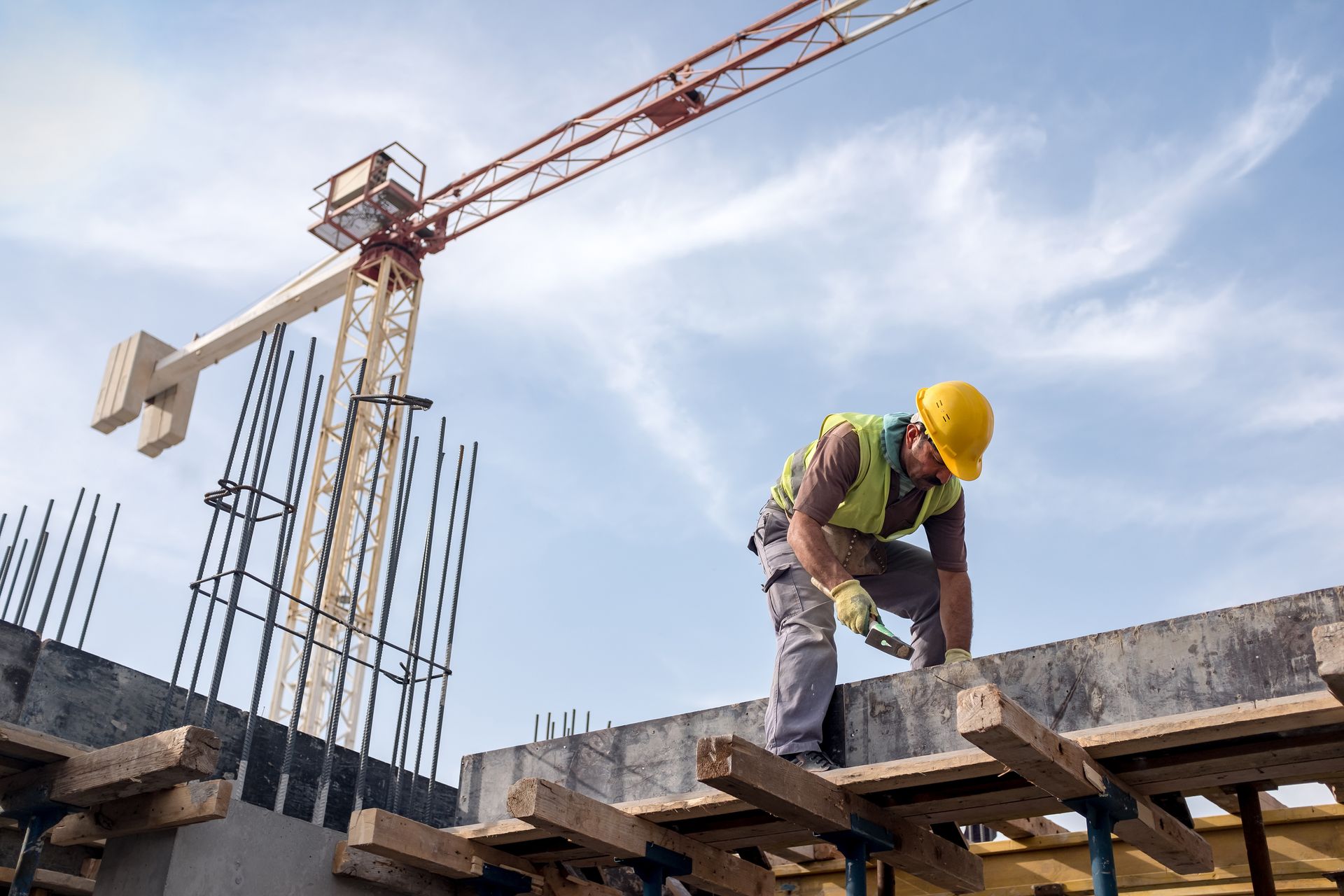